IMPACT
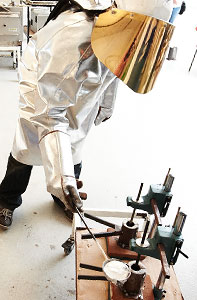
Improving the Melting operation for higher Performing Aluminium ComponenT (IMPACT)
Introduction
Up to 30% of all aluminium products manufactured worldwide are used for shape casting products. Industries continuously searching for solutions to lower mass without compromising the application's efficiency. One of the most important elements that limits the mechanical performance of an aluminium cast product is casting defects (e.g. porosity, oxide films and inclusions). A large portion of such defects are initiated during melt preparation process. This project aims to expand the knowledge on the mechanism of defect formation in the value chain from raw material to finished product with focus on the melting process, melt transport and transfer to the die. The ambition is to reduce the level of defect in different steps of melt operation.
Purpose
This project aims to evaluate the effect of various operation steps (raw materials, melt cleaning, melting furnace, melt transport and transfer, melt holding furnace) on the melt quality and subsequently their effect on the productivity of the foundry and post treatments as well as mechanical performance (fatigue life) of the cast component.
Expected results
End users are industries who use cast components in automotive industry and frames of outdoor luminaires. Each component needs to withstand certain strength in order to meet the requirements in their applications. Presence of undesired features which were originated from poor melt quality results in pre-mature failure and shorten the component life cycle. Improving the soundness of the melt which is aimed in IMPACT project results in increasing the load bearing capacity of the cast component. The end-users are provided by the opportunity to utilise the components with improved properties, as thinner sections which lower the gross weight of transport and hence reduce CO2 emission. In another prospect, increasing the load bearing capacity of the component enhances performance of component (increased threshold strength) offering longer life cycle.
Collaboration partners
- Bryne AB
- AGES
- Fagehhult
- Nordic Furnace AB
Project duration and financing
The project funded by VINNOVA, started from November 2019 and will be for three years.
Contact information
For more information, please contact Mohammadreza Zamani.