LeanCast
Facts
Academic Partner: School of Engineering
Industrial Partners: Scania CV AB, SinterCast AB, Volvo Group Technology AB, SKF Mekan AB
Duration of the Project: 2018-2022
Research Team:
Attila Diószegi (Projectleader)
József Svidro
Vasile Diaconu
Taishi Matsushita
Ilia Belov
Peter Svidró
Judit Svidró
Dinesh Sundaram
Björn Domeij
Juan Carlos Hernando
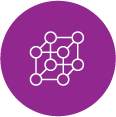
Based on today's climate-related challenges, the core question of this research project is: How can we enable and control a sustainable design and production of cast iron components? The full title of the project is "Lean and sustainable design and production of cast iron components".
Introduction
Cast iron is one of the most environmentally friendly technical alloys used for complex automotive applications with respect to the production process and lifetime application. The material is fully recyclable, which contributes to a low environmental footprint.
The sophisticated production process for cast iron, which includes melting and casting, contributes to variation in the material properties and may cause defect formation. This limits the component life time and causes excessive use of natural resources related to the production process.
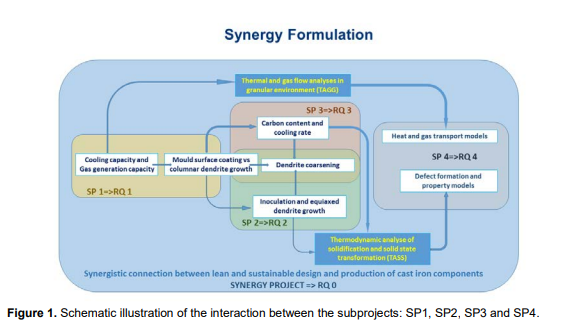
Purpose
The aim of Lean Cast is to extend the knowledge frontier within design and production of cast iron components with a comprehensive focus on reaching an environmentally sustainable process.
The solutions developed within the project will primarily lead to increased material utilisation in the casting, reduced amounts of consumed natural resources like metals, sand and minerals, shortened development time for improved cast products, and prolonged lifetime of the components by optimisation of the production process parameters and material properties.
Lean Cast is a synergy project with several subprojects focusing on form material, defect formation, material properties, and modelling and simulation of phenomena arising during casting.
Expected results
The outcomes from the project are expected to be:
- models to instantaneously predict the production parameters
- models to predict material properties and component defects
- methods to deliver input data for property and defect prediction
- demonstrators enabling design and process control
- guidelines on how to implement the obtained results into the industrial practice
Collaboration partners
- Scania CV AB
- SinterCast AB
- SKF Mekan AB
- Volvo Group Trucks Technology AB
Project duration and financing
- The project runs between 1 September 2018 and 31 January 2022 and is co-funded by the Swedish Knowledge Foundation (11,07 MSEK), Jönköping University (3,27 MSEK), and the collaboration partners (11,07 MSEK).
Do you want to know more about the project?
- Professor Foundry Technology
- School of Engineering
- attila.dioszegi@ju.se
- +46 36-10 1656
Do you want to develop the next project with us?
- External Relations Manager
- School of Engineering
- linda.bergqvist@ju.se
- +46 36-10 1074